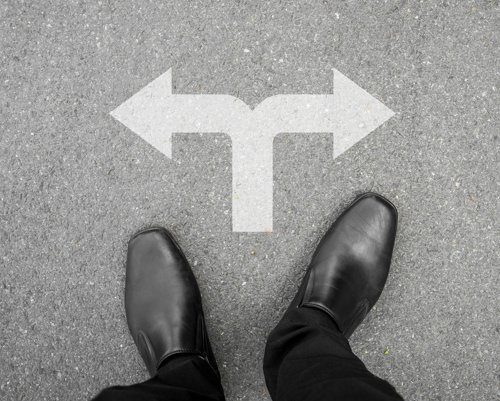
2 Types of Human Errors…
According to the Health and Safety Executive (HSE)… human errors can be active or latent.
Active failures are direct and immediate causes of an accident, and are usually made by front-line staff such as drivers or machine operators. There are 3 types of active human error:
- Slips and lapses – made inadvertently by experienced operators during routine tasks;
- Mistakes – decisions subsequently found to be wrong, though the maker believed them to be correct at the time; and
- Violations – deliberate deviations from rules for safe operation of equipment.
Familiar tasks carried out without much conscious attention are vulnerable to slips and lapses if the worker’s attention is diverted: for example, missing a step in a sequence because of an interruption. Mistakes occur where a worker is doing too many complex tasks at the same time, or is under time pressure; for example, misjudging the time and space needed to complete an overtaking manoeuvre. Violations, though deliberate, usually stem from a desire to perform work satisfactorily given particular constraints and expectations.
Latent failures are those aspects of an organisation which influence human behaviour and make active failures more likely. Factors which contribute to human error include:
- Job – distractions, lack of time, inadequate procedures, poor lighting or extremes of temperature;
- Human – physical ability, competency, fatigue, stress or drugs;
- Organisational – work pressure, long hours or insufficient supervision; and
- Plant and equipment – poor equipment design or workplace layout.
Although not all mistakes can be anticipated, companies owe a duty to prevent or control factors which make human error on the part of their workers more likely. The Court of Appeal in Polyflor Ltd v Health and Safety Executive [2014] held that employers can even owe a duty in certain circumstances to take reasonable steps to protect employees from risks caused by their own foolish acts.
What this means for you
Individual risk profiling is vital: organisations with increasingly automated environments face different risks to those where work is carried out by people alone. Companies need to take steps to limit the consequences of their employees’ human error, always bearing in mind:
- The fact that no accidents have occurred yet is no indication that working practices are safe;
- Human error must be seen in the wider context of the organisation and its management;
- If latent failures are not addressed, the probability of repeat accidents will remain high;
- Since one latent failure can lead to several possible errors, removing latent failures is extremely cost-effective;
- Risk assessments must be individually tailored and regularly reviewed;
- Safety policies are ineffective unless they are properly resourced, implemented and reviewed; and
- An organisation’s commitment to safety must be led from the top down.
Companies should aim to introduce the following:
- Measures to eliminate risk, such as using inherently safe products;
- Measures to combat risks at source, such as the provision of machinery guards; and
- Measures to minimise risk relying on human behaviour, such as safe working procedures and the use of personal protective equipment.
By Anne Davies, Special Counsel and Head of Health & Safety and Christopher Adams, Paralegal, Withers LLP. As published in SHP (Safety & Health Practitioner) online article “To err is human: human error and workplace safety”.