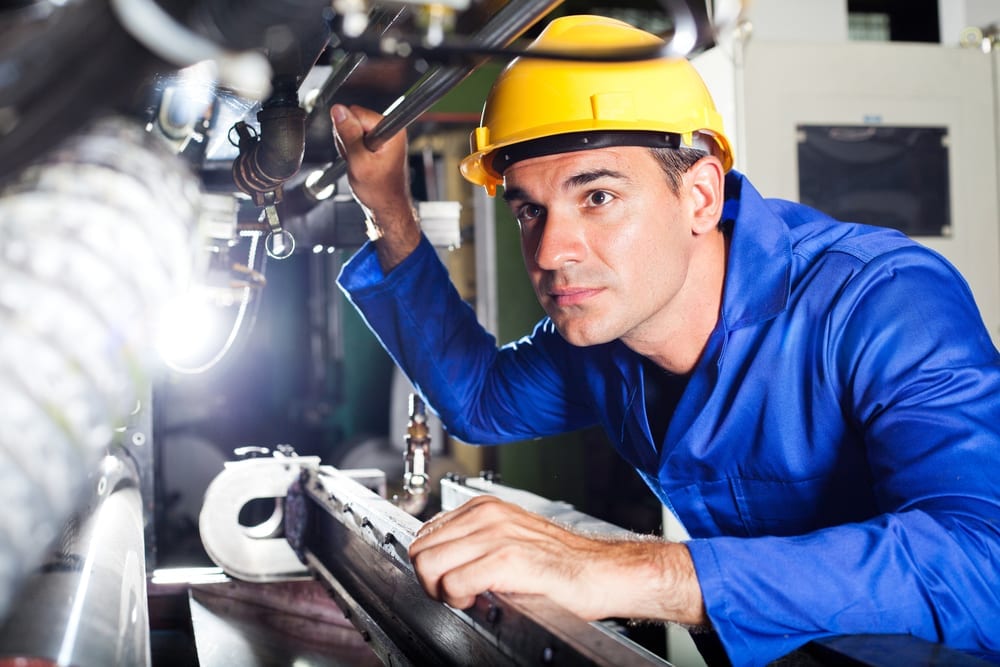
Human Error Investigation Step 2: Is it training? It depends.
If you have been following, we are going through the process of the Human Error Investigation Process. You can check previous blog posts: “Why you need a Human Error Investigation Program?” and “Human Error Investigation Step 1.”
So, now that we know how to determine the types of error let’s get to work!
For us to establish if the error is related to training, we must find out if the failed action was due to a lack of knowledge (did not know what to do), lack of skill (did not know how to it), or lack of ability (could not do it). If the deviation does not meet these criteria, it is NOT training related.
Is this event related to training? Let’s see a case.
Case #HES001
Human Failure: The operator opened valve #15 out of the pre-established sequence creating a chain reaction that ultimately delayed the release of the batch.
Investigator: Claudia Quest
Erratic Human (technician): Herriberto Prone
The interview: All the investigations must include a conversation either with the person that made a mistake or some other Subject Matter Expert (SME) that can provide all relevant information about the task under investigation. Start by asking what happened or what do they think happened, and try to do the interview where the event took place. We will dedicate a separate article with details about the interview process in a future publication. The quick summary below.
Claudia: Tell me what happened? (Open question)
Herry: I was following the procedure, the instruction #17 to be precise. It clearly says: Make sure valve 15 is in the open position, but when I got there it was closed. So, I opened it. I really did not know what to do in that situation, so I thought if it said to assure it’s open, well, I had to make sure it was open (Interpretation due to lack of information).
Claudia: Is it the first time you perform this activity? (Closed for clarification)
Herry: No, I do it all the time, it’s just that it is always open; so, I did not know what to do. Thought that was the right decision.
Ok. Now that we “kind of” know what happened here let’s start:
Type of error: Intentional Error of Commission: Decision to open the valve (No harm intended) due to:
- Lack of knowledge: Training related in which case you could re-train and explain what to do in that case.
- Lack of information: Instruction missing in which case you can include a conditional statement in the procedure with the possible scenario.
This means training is one possibility. Remember you get information from different sources like labels, charts, signs, procedures, and batch records. Now let’s see if training is the best way to solve the problem.
The root cause path towards Root Cause Determination: Based in the Root Cause Determination Tool.
Scenario #1
Category: Training
If you trust that people will make the right decision on their own, then train and address the lack of knowledge. Then the Root Cause Code (based on the RCDT) will be C5c11. See below.
C: Human Performance Problem (problem type)
5: Training (category)
c: Training/Content (near root cause)
11: Abnormal events training (root cause)
= C5c11
CA: Re-train and re-qualify
PA: Evaluate all (OTHER) critical tasks and activities and make sure all are trained and qualified in abnormal/non-routine activities and steps.
Scenario #2
Category: Procedures
The second option will be to include a conditional statement in the procedure. This is recommended, especially for a critical step. In this case, the Root Cause Code will be:
C: Human Performance Problem
4: Procedures
c: Wrong or Incomplete
04: Incomplete, situation not covered.
= C4c06
CA: Include a conditional statement in the procedure, e.g., IF that valve is closed, THEN call the supervisor.
PA: Perform a what-if analysis of critical procedures, activities, and steps and include conditional statements where needed.
So, is it training? It depends.
There you go. If you want us to cover a particular topic or a hypothetical case (wink, wink) write us!