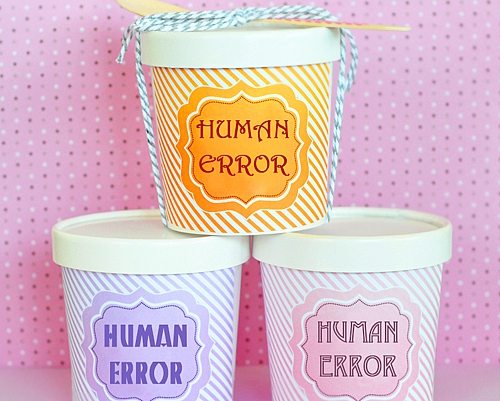
Many flavors of Human Errors
The concept of error that many are familiar with comes from tests taken. A wrong answer represents an error. In general, a wrong answer comes from not knowing the right answer… The concept of error in human error reduction in manufacturing is much broader.
There are many instances in which an error occurs, and everyone knows that it is an error. And, in fact, everyone knows the right answer. So why was the error made? Answering that question is at the heart of human error reduction techniques. And there are many possible answers.
Listed below are a few:
- Poor lighting or other environmental impediments
- Fatigue
- Communication failures
- Excessive workload
- Deliberate overriding of established procedure
Clearly, assigning someone additional training when the cause of his or her error was poor communication or poor workplace design will not resolve the cause of the error, though it might appear to satisfy regulatory requirements.
Digging Deeper
The primary goals when investigating an incident are to discover what caused it and why — with the eventual goal of making sure it does not happen again. Whether that means going all the way back to the root cause, or merely breaking the chain of events so the problem cannot recur, is a decision that companies must make on each occasion.
At first blush, an adverse event may look as though it was caused by human failure, but investigations frequently reveal that a much deeper issue is to blame. According to industry analysts, in the majority of adverse events, the organization contributes to the incident by setting employees up to fail. RCA allows an investigative team to go far beyond the surface causes.
The recommended levels of an investigative analysis, starting at the uppermost level and digging down to the lowest are:
- Human error or equipment failure
- Task control issues
- Process control issues
- Management system issues
- Organizational cultural issues
If only the top levels of an event (human error or equipment failure) are investigated, only one problem will be solved. The deeper a company digs into the event, the more the investigation will learn about organizational problems. Consider the following example:
A fuse blows and causes the lights to go off. A company can identify the immediate causal factor — “fuse blew” — and replace the fuse. It can also identify another cause — “a short” and repair the wire that shorted. If it doesn’t identify and correct the factor that led to the fuse blowing, however, (e.g., wiring not maintained because there was insufficient maintenance), other systems may experience similar failures.
RCA seeks to identify these deeper systemic problems, such as lack of an adequate maintenance budget, and correct them. Unfortunately, some RCA methods fail to dig far enough. Oftentimes, organizations will get down to the management systems level and stop at that point primarily because corrective actions and recommendations must be actionable and measurable and it may be difficult to do that at the organizational cultural level.