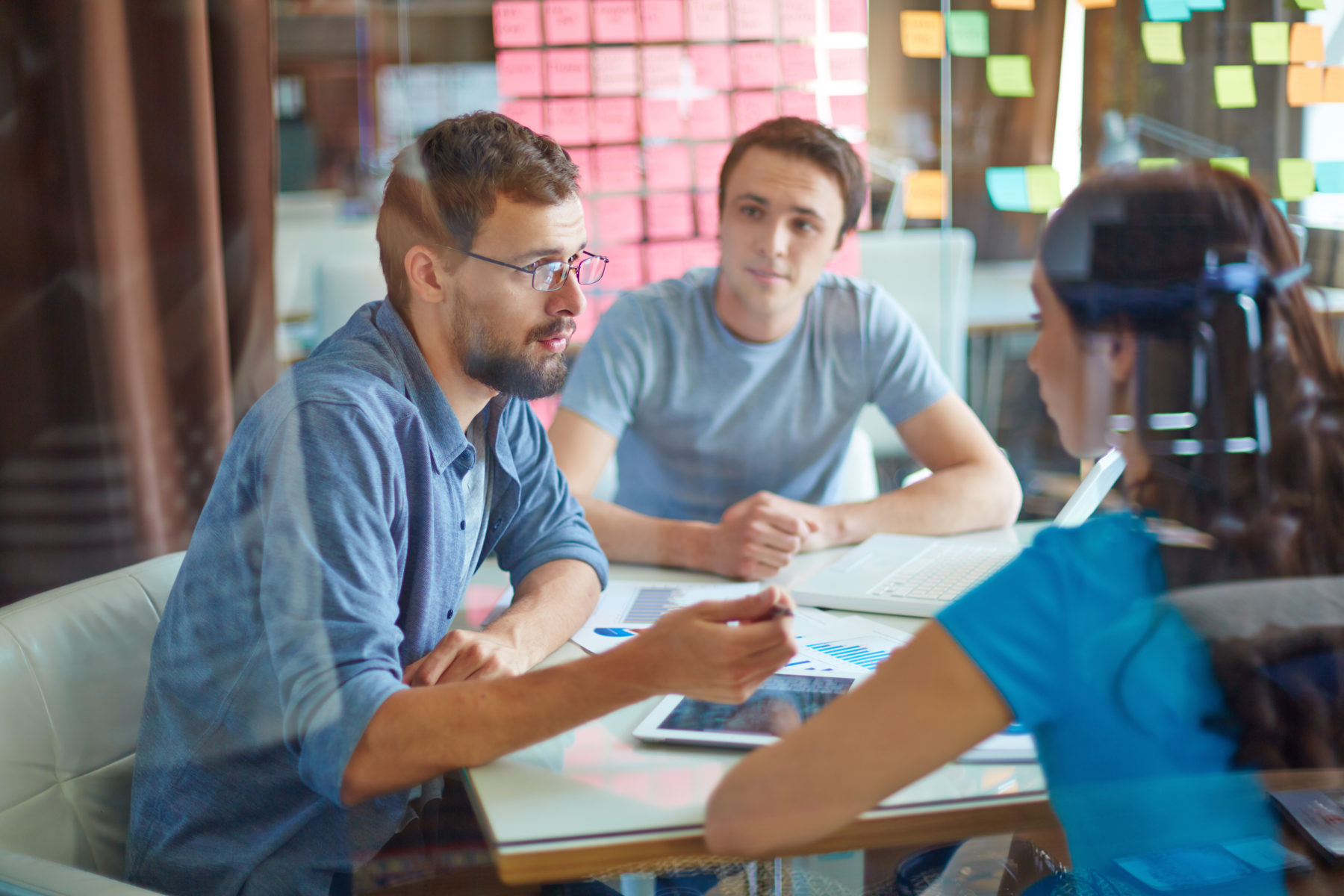
Types of Human Error You Should Beware of in Your Workplace
Human errors account for approximately 23% of unplanned downtimes in manufacturing. As a manager, figuring out how to reduce human error in manufacturing should be on top of your priority list to ensure you keep up with your operations running optimally. To effectively reduce human errors in your workplace, you must first understand the types of human errors that can occur in your manufacturing practices.
Here are the different types of human error that can occur in your workplace.
Skill-Based Errors
These are unintentional errors caused by negligence or when a worker is distracted by internal or external factors. Internal distractions are factors that affect the cognitive functioning of an employee and trigger cognitive load errors. For instance, high stress levels or work burnout may cause a worker to lose concentration midway through a task. External distractions are mostly physical and work-based factors such as too much noise in the workplace or a worker being distracted by the phone. All workers are vulnerable to making skill-based errors regardless of their experience.
The two main types of skill-based errors are slips of action and lapses of memory. Let’s explore them further.
Slips of Action
A slip of action is when a worker does an unintended action or fails to do what’s supposed to be done. These errors are caused by attention failures when a person is on autopilot. Examples of slips of action errors include omitting one or two steps in a task, using the wrong equipment for a task, pressing the wrong button, recording the wrong values, applying too much or too little force in a task, and executing an action too soon or too late. Slips of actions can cause your business untold losses, especially in a complex field like manufacturing.
Lapses of Memory
This happens when a worker forgets to execute an action in a routine task. For instance, a construction worker may forget to fasten scaffolding, or a packer may forget to seal an item after processing is done.
Slips and lapses occur when workers are distracted and interrupted, when there are two confusing tasks, when workers give little thought to the task because they’re familiar with it, or when the tasks are long-winded and complicated. You can rely on human error prevention training and tools to reduce slips and lapses errors in your workplace.
Mistakes
Unlike skill-based errors that are unintended actions caused by internal and external distractions, mistakes are caused by poor planning because a worker is inexperienced or relies on inaccurate information. The two main variations of mistakes are knowledge-based and rule-based mistakes.
Knowledge-based mistakes occur when a worker has inadequate knowledge of how a task should be executed. For instance, a new clerk may feed the wrong code numbers to a labeling system and have poor product labeling. Rule-based mistakes occur when an employee applies the wrong rule in a task or disregards a standard operating procedure.
Human error reduction training can help you to effectively prevent and reduce knowledge-based and rule-based mistakes in your workplace.
Violations
Of the three types of human error, violations are the intentional failures caused by employees with full knowledge of the rules and operating procedures. Violations are categorized into two — situational and exceptional. Situational violations occur when employees feel they have no choice but to do the wrong thing because of their situation or when they want to bypass a rule. Exceptional violations refer to when workers intentionally do the wrong thing because they are not afraid of the consequences or believe they are immune to the consequences. Mostly, violations indicate that someone, particularly a unit supervisor, is slacking at their job.
While these types of human error are common in a workplace, they are fully preventable if you invest in human error prevention tools and training. Today, manufacturing regulators no longer accept human errors as a justifiable cause for manufacturing malpractices. That’s why it’s a good idea to invest in human error reduction training and tools in your workplace.