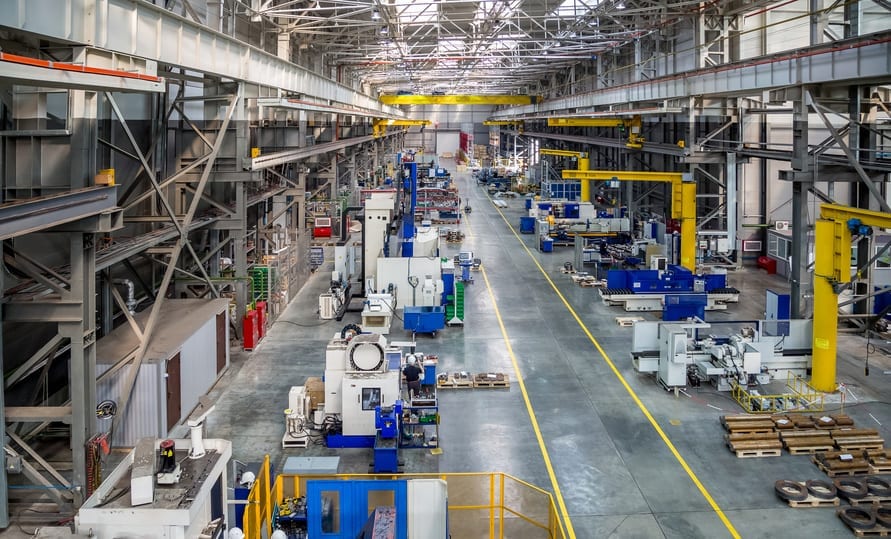
5 Ways of Reducing Human Error in Manufacturing
Human error is a common occurrence in all organizations. For example, Amazon experienced an outage in 2017 due to human error. Another example is the cancellation of flights due to data center outage in British Airways in 2017. These errors led to a massive loss for both companies.
Human error involves some kind of miscommunication and failing to follow written procedures. For instance, in a pharmaceutical lab, there is a procedure to be followed when manufacturing drugs. Unfortunately, an employee might assume they have mastered the process, quantity requirements, and proceed to mix the elements.
Taking disciplinary action against that person, however, can’t rectify the mistake or prevent future errors. It is, therefore, essential to develop measures that will help in reducing human error. Approximately 23% of unplanned downtime in production is caused by human error. Fortunately, these errors can be reduced. Let’s look at the tips on how to prevent human error in the workplace:
1. Consult Companies Offering Human Error Solutions
Every business has a weakness, but that weakness shouldn’t be your employees. Not equipping your employees with the tools and knowledge needed for minimizing different types of human error is a weakness that can ruin an otherwise successful organization. Rather than waiting until an error occurs, consult a human error solution provider and seek GMP training for error prevention.
Interestingly, you can take the CAPA training online. You only need to spare your time and learn why and how your work should be done to prevent errors.
2. Focus on Proper Communication
The second important factor for reducing human error is maintaining effective communication throughout your organization. Look at it this way: if you’re too harsh with your employees, it’ll be impossible for them to ask questions relating to certain aspects of the job. Inevitably, they’ll proceed with an erroneous action causing all kinds of organizational issues.
Ensure there is a healthy dialogue between seniors and junior employees and address any breakdown in communication as proactively and professionally as possible.
3. Refresh the Regulatory Compliance Courses
Regulatory compliance courses are slightly expensive, and employers might overlook them. The truth is, they contribute significantly to an organization’s bottom line. Taking these courses helps in reducing human error because employees will continually learn how to prevent and correct them. They are also provided with tools to enhance their preventive skills.
4. Publish and Print Job Steps
With so many things that need to be done during the workday, it’s understandable for them to have a memory lapse. In that context, post the procedure of every job operation near the working area to help in reducing human error. For example, if it’s a control room, ensure there is a procedure to be followed posted on the wall.
5. Supervise
The supervisor should be out in the working area as much as possible — not just hidden in a back office. Checking on how employees are working gives you a chance to identify whether they’re using shortcuts to achieve a goal, potentially leading to errors. However, the supervisor shouldn’t be unapproachable because employees might panic after seeing the supervisor and cause an accident. So put on a smile, and reassure your staff that you’re there to help and not reprimand.
Train, Communicate, and Partner with Human Error Solution Provider
Reducing human error is a process. It can’t be achieved in one day. You have to continually refresh the skills you learned and communicate effectively. It’s after following the steps that you can minimize downtime across the manufacturing sector.