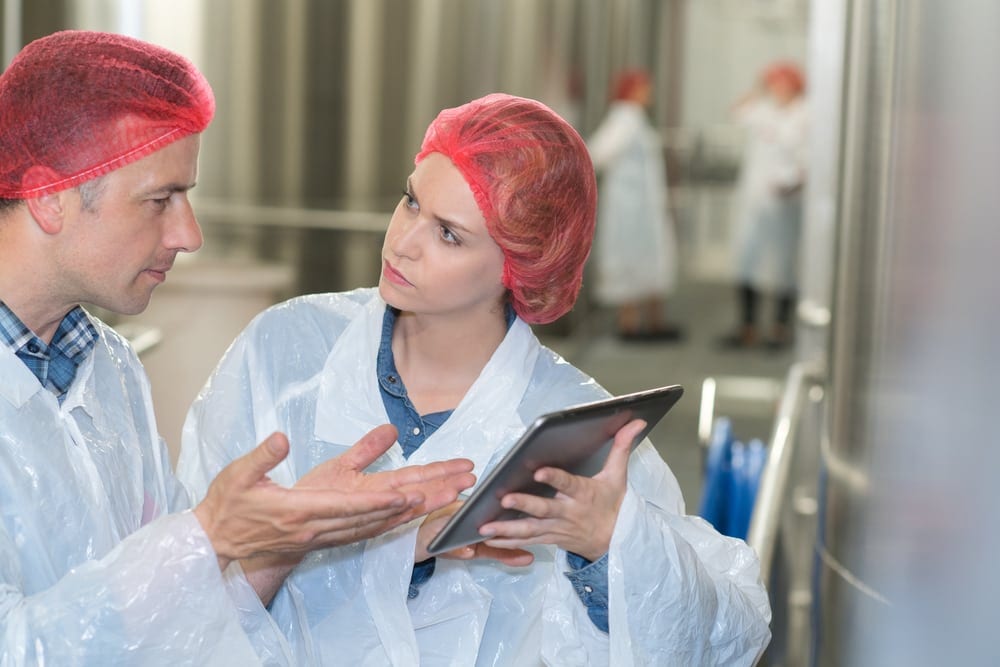
Why you need a Human Error Investigation Program? Because it’s not optional; it’s a requirement.
If you work in the GMP regulated industry you not only need to address human error deviations because they are an inconvenience, you must do it because the regulation requires it. Oh, you don’t believe me? Let’s look at two different examples:
- The CFR – Code of Federal Regulations Title 21 Subpart B_Organization and Personnel Sec. 211.22 talks about the “Responsibilities of quality control unit.” and it states that “(a) There shall be a quality control unit that shall have the responsibility and authority to approve or reject all components, drug product containers, closures, in-process materials, packaging material, labeling, and drug products, and the authority to review production records to assure that no errors have occurred or, if errors have occurred, that they have been fully investigated…”
Now, let’s look specifically at this section of the sentence: “if errors have occurred, that they have been fully investigated, meaning until the root cause of the error is found, so no, Human Error is NOT a root cause. Still not convinced? Let’s move to number two:
- The European Commission is a little more specific when in “The Rules Governing Medicinal Products in the European Union, Volume 4, EU Guidelines for Good Manufacturing Practice for Medicinal Products for Human and Veterinary Use” in section 1.4 states that “A Pharmaceutical Quality System appropriate for the manufacture of medicinal products should ensure that: (xiv) An appropriate level of root cause analysis should be applied during the investigation of deviations, suspected product defects, and other problems…” then it continues “Where human error is suspected or identified as the cause, this should be justified having taken care to ensure that process, procedural or system-based errors or problems have not been overlooked, if present. Appropriate corrective actions and/or preventative actions (CAPAs) should be identified and taken in response to investigations. The effectiveness of such actions should be monitored and assessed, in line with Quality Risk Management principles.”
Ok, “appropriate level of root cause analysis” (fully investigate) sound familiar? And then it goes as far as to specifically say that even if there is a suspicion (hypothesis) where human error is the cause (not the root cause but a causal factor) “this should be justified” (make sense) ensuring that process, procedures and systems are to be variables that need to be factored-in when explaining human failure. Did the human fail because process weaknesses set them for failure? Do procedures provide for all information and clearly indicate critical steps and warning or cautions associated to steps? Do systems work for manufacturing or is it the other way around? These are all tough questions to ask, but most importantly answer.
So yes. To comply with this regulatory requirement a human error investigation program can now be perceived as a non-negotiable GMP requirement, but bear in mind that the spirit of the regulation is not referring only to the investigation process, but the actual results. Being able to identify the root cause of the error, correct, it, prevent ed and measure its effectiveness is not only a smart productivity and business idea; it’s your responsibility.
However, fear no more! You are not alone. In the next newsletters and blog posts, I will share how to start and get your Human Error Solutions boat sailing. I will discuss how to create your baseline metric, how to get to the real human error root cause and how to get tangible results in less than a year.
Now, do you want to fix the blame or fix the problem? I figured. Let’s get this “ship” together.