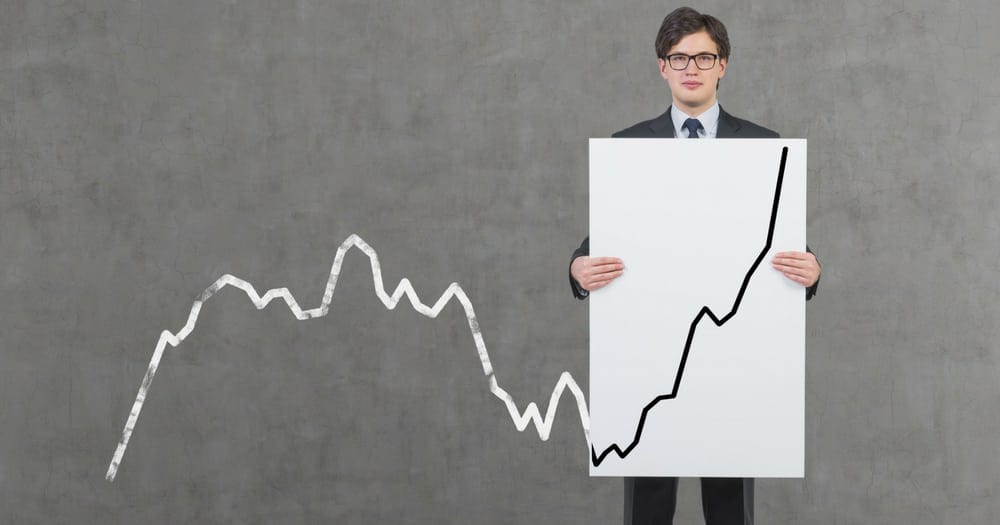
Human Error: Tracking and Trending
Past errors, if they are not found and fixed, are often predictive of future mistakes. This is why companies must track and trend errors in the manufacturing environment. The causes of the errors must be identified, categorized and analyzed so that they can be dealt with in a systematic way. For instance, if it determined that most of a company’s errors stem from poor SOPs, then the company can put a revision of its SOPs at the top of its action plan.
Although tracking and trending errors is a good way to combat them, it isn’t always easy to decide what to track and trend and when. The tendency among drug manufacturers is to rank issues or areas from major to minor. Companies identify what they believe are important and not so important trends — and those things that might not be trends. It is important to select items with major impact on the company, especially product and process-related items. The FDA tends to focus on three areas of risk: patient risk, product risk, and process risk.
The extent to which, and when, a company conducts trending depends on the impact of the issues. The level of risk associated with an issue and its impact on a business is the way to evaluate and determine how frequently trending should be done and whether an area makes it to the top of the list. The things that offer insight into major risks should be trended first and most often. For example, complaints often constitute an area that should be regularly addressed, even if some of those are not particularly important because they deal directly with patients — a high-risk area.
Management must review all data trends. Trends should be reported so that management hears first about those trends that are occurring most frequently, as well as those that pose the greatest risk to the company, the products, and the processes, but first and foremost, to the patients.
Management review should be conducted at a level of frequency that is based on the kinds of problems being detected. As time goes by and the problems are better controlled and the level of risk falls, the reviews may be conducted less often. In other words, look at the array of products being produced and, as products age and new products are introduced, consider the correct frequency.
Management must ensure that each corrective or preventive action that is taken is appropriately implemented and verified or validated. The process should include identifying problems, recommending solutions and verifying that those solutions are successfully fixing the problems. All of these procedures must be properly documented for internal recording purposes.